SOLUTION STORY
STEEL INDUSTRY SOLUTION 鉄鋼業界向けの大型ギヤの調達
PROJECT OVERVIEW プロジェクト概要
椿本興業にとって、過去最大規模を誇った大型ギヤの調達。
これまでに経験がないプロジェクトであったがゆえに、製品の品質基準を満たす厳格な工程管理や、
各種法律を調べた上での速やかな搬入プランの作成など、数々のハードルを乗り越える必要があった。
前例のないプロジェクトを遂行するため、社内外の垣根を超え、各分野のプロフェッショナルが結集した。
プロジェクトの陣頭指揮をとったメンバーが、当時を振り返る。
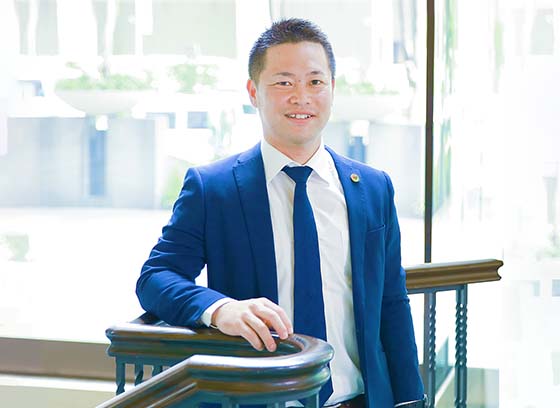
PROFILE
動力伝達事業
池田 和之Ikeda Kazuyuki
2007年入社。機械部品の提案をはじめ、動力伝達部品における特殊部品も手掛ける動力伝達事業を担当。仕入先は国内だけではなく、韓国、中国、台湾、フランスまで足を伸ばし、最適な商品を提案している。今回の大型ギヤのプロジェクトにおいては、メンバーの中心として製品の納品・稼働まで携わった。
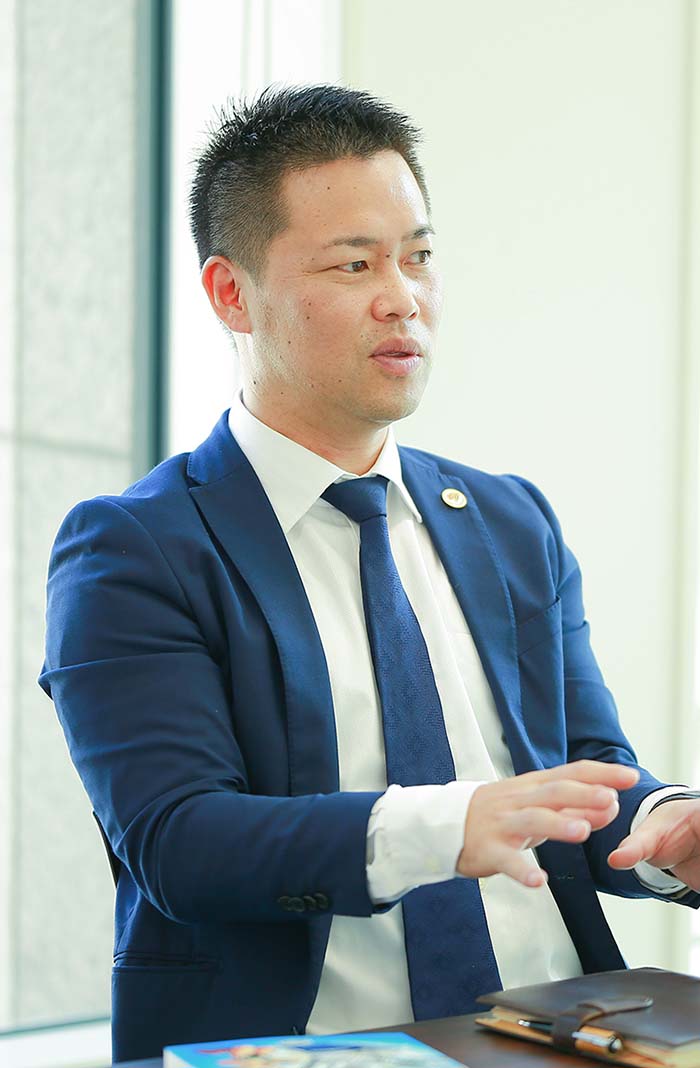
国内外を越えたネットワークが、
大型プロジェクトを引き受ける糧に
こちらのプロジェクトがスタートした経緯について教えてください。
当時、担当していた大手の製鉄メーカー様から、金属の「圧延」に使用する大型ギヤを調達したいとのご相談を受けました。
大きさは、直径1.2メートル、長さ6メートル。重量は30トンという、これまで当社で経験がないほどの大型ギヤでした。
これだけ大きなギヤを製造できるメーカーは国内では少ないため、お客様が求める品質基準を満たす海外の調達先を見つけるところからプロジェクトはスタートしました。
では、製作できるメーカーを探すところから着手されたのですか?
実を言うと、これまでに国内外を問わず、幅広いお付き合いがあったので、ご相談を受けた段階で台湾とフランスのメーカーであれば対応できるだろうと見当を付けていました。そのため、加工技術などを検証し、台湾の大手メーカーで加工することに決めました。ただ、次に課題となったのが、どこから材料を調達するかということです。
どのようなポイントを踏まえて、材料の調達先を探されたのですか?
ここでサポートしてくれたのが、鉄鋼関係に詳しく海外との幅広いネットワークを持つ社内のテクニカルアドバイザーでした。海外のあらゆる材料メーカーを洗い出し、その中から韓国の材料メーカーに相談することになりました。
アドバイザーと共に現地へ赴き、大型ギヤの材料にあたる鉄の塊(インゴット)の熱処理の方法や、規格に基づいて製造できているのかなど、あらゆる視点から品質をチェックし、最適なメーカーかどうかを検証しました。
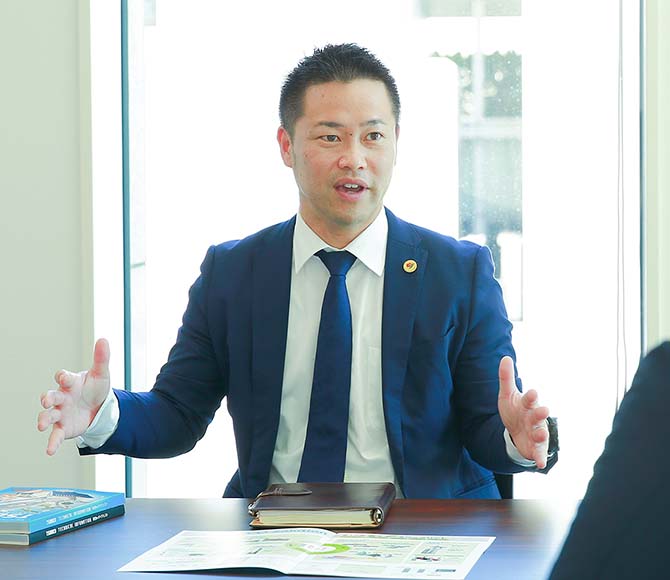
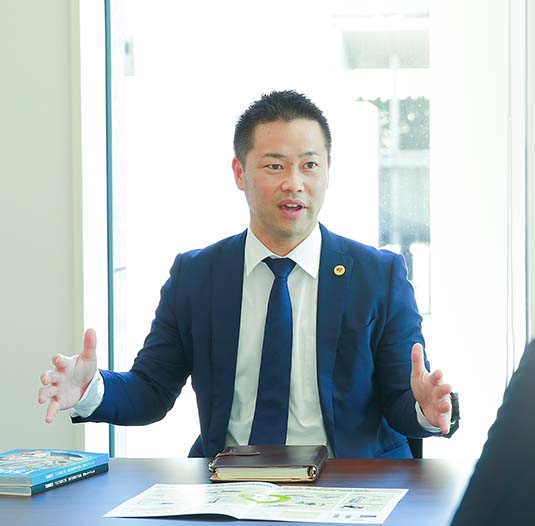
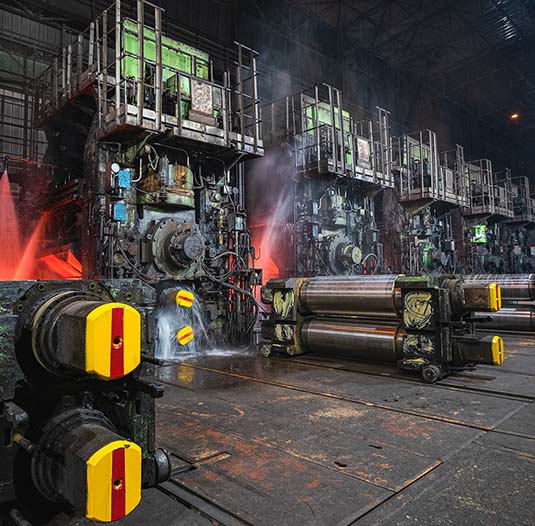
従来以上の精密さが求められ、
新たな品質チェック体制を構築
材料を作る過程で苦労された点はありましたか?
従来以上の品質管理の難しさに直面しましたね。韓国メーカーにおいても、それほど大規模なインゴットを製作するのは例が少なく、これまでの経験に加え、様々な試行錯誤をしながら製作することになりました。
ただ、それは私たちも同様だったため、思いもよらない品質の不具合も発生しました。
その原因は何だったのですか?
最初は何が原因か分からず、異なる製造方法の検討や文献を調査し、さまざまな可能性を探っていきました。そこで、思い当たったのが、品質管理の精密化です。これだけ大規模になると従来よりもさらに精密なチェックが必要ということが分かりました。そこで、ゼロから製造過程を見直そうと、工程を全て洗い出し、1つ1つの工程を細分化。より細かい品質チェック体制を作り上げ、無事に品質基準を満たすインゴットを製造できたのです。
なるほど。
では、次の段階である台湾メーカーでの加工はどうでしたか?
加工は滞りなく進みました。それ以上に、配慮が必要だったのは製品をどのようにお客様に納品するかという問題でした。
日本の道路は、法律で定められた重さのトラックしか走ることができないため、30トンもの製品を運ぶのは容易ではありませんでした。
どのような方法で納品されたのですか?
製品をパーツごとに分解した上で輸送し現場で組み立てる方法や、そのほか、色々なプランを検討していきました。その時、力を貸してくれたのが当社の貿易部門でした。これまで数々のプロジェクトを手掛けてきた経験から、あらゆる手立てを模索し、船で台湾から日本まで輸送した後、特別に走行できるルートを手配してくれたのです。これで、あとは現場で稼働させる作業だけになりました。
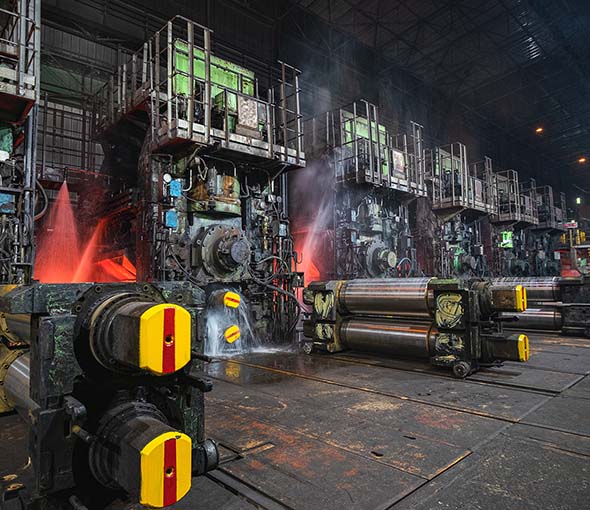
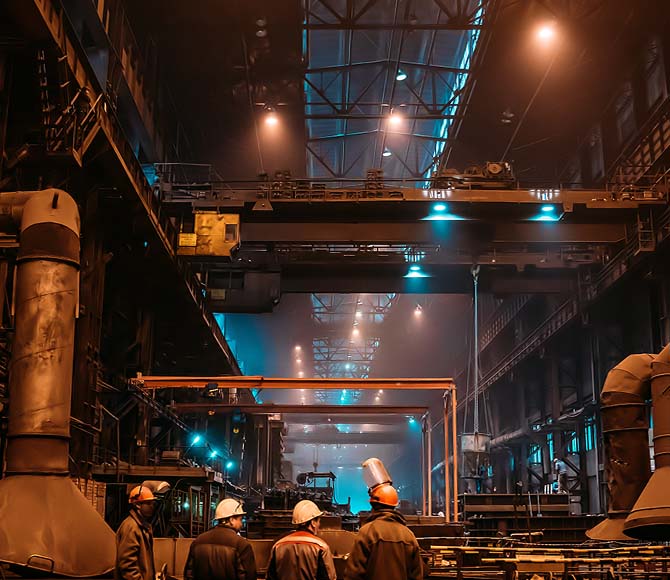

社内のテクニカルアドバイザーや
台湾メーカーと国境を超えて連携し、
専門家の知見を結集
製品を稼働させる段階では、
どのような方々が現場に立ち会うのですか?
テクニカルアドバイザーと台湾メーカーのスーパーバイザーに立ち会ってもらいました。これだけ大きな製品を設置すると、その重みで本体が沈んでしまいます。
それを加味した上で、設置方法を検討・指示してもらい、稼働時にトラブルが発生しないようにチェックしていきました。この体制で、お客様ともひとつずつチェックを繰り返しながら夜通し作業を行い、無事に納品から稼働までを終えられました。
プロジェクトの立ち上がりから稼働までは、どれくらいの期間がかかったのですか?
およそ2年です。ちょうど、使用されていた大型ギヤの更新時期が近づいていたこともあり、なんとか納品に間に合い、お客様にとても喜んでいただきました。あとから話を聞くと、このプロジェクトでは当社の他に何社かご相談をされていたようですが、「納期にきっちりと間に合わせます」と回答したのが当社だったことから、ご発注していただけたとのことでした。ですので、余計にしっかりと終えられて私自身も嬉しかったですね。
このプロジェクトを終えた後も、取引額の大きなご依頼が続いたので、お客様にも満足していただけたと感じています。
色々と乗り越えなければいけないハードルがあった中で、池田さんが最後までやり遂げられた理由は何ですか?
一番は、これまでお取引があったお客様の期待にお応えしたいという責任感。
そして、プロジェクトを力強くサポートしてくださった社内外からの支えのおかげで、迷うことなく最後まで突っ走ることができましたね。
これは、私だけではなく社内に根付く文化だと思います。
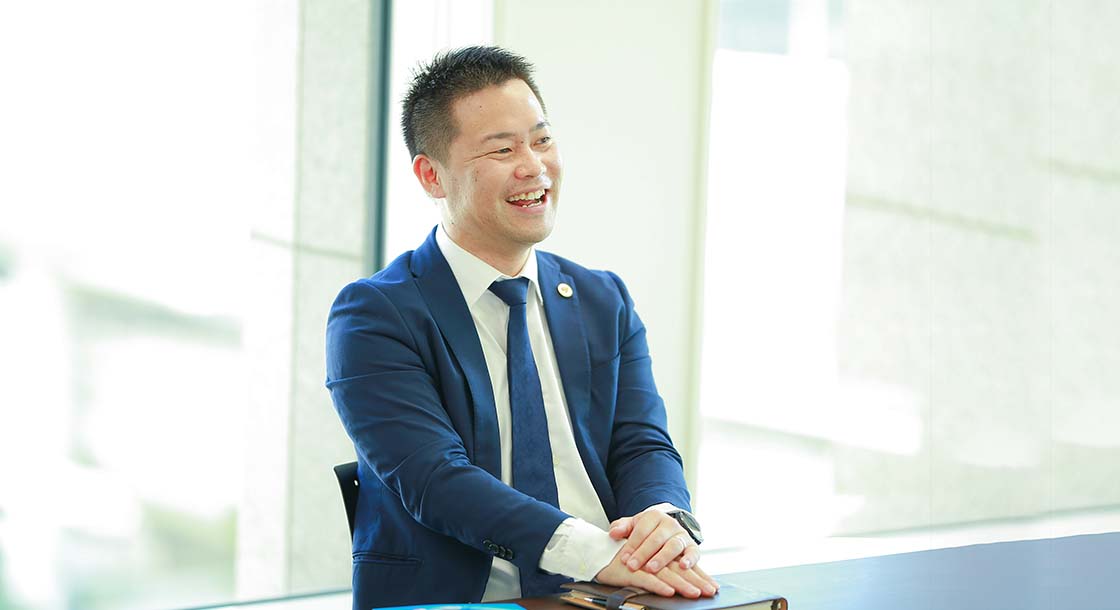
最後にこの経験をもとに、今後はどんなプロジェクトを手掛けたいと思っていますか?
こうした大型プロジェクトを経たことで、少々のことでは動揺しなくなりましたし(笑)、品質管理に関する知識も格段に向上しました。
今後はそのスキルを活かし、ご提案する製品の精度を高めることや、当社が経験したことがないような新たなプロジェクトにも挑戦していきたいですね。